Windräder-Produktion
Bei der Energiewende fliegen die Funken
Bei Bremerhaven entstehen Fundamente für Offshore-Windräder. Wir haben die Produktion besucht.
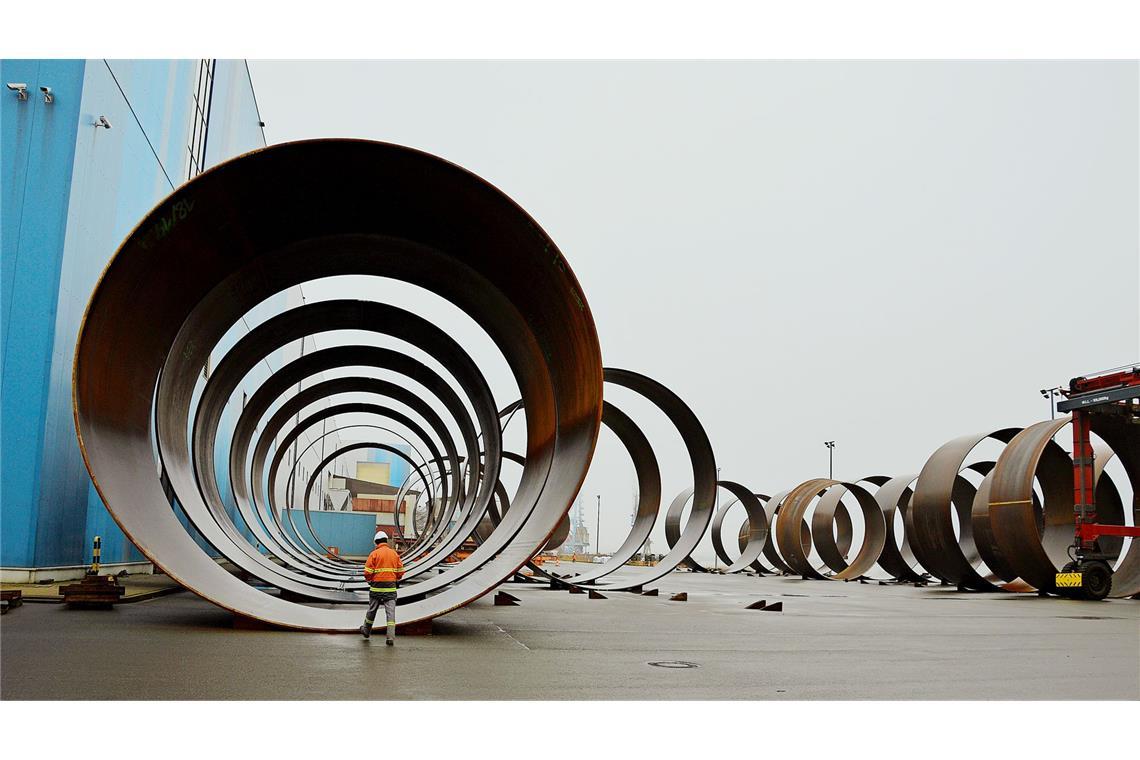
© Phillipp Steiner
Sogenannte Mantelschüsse aus Stahl mit Durchmessern bis um die zehn Meter. 30 Mantelschüsse ergeben ein Fundament.
Von Phillipp Steiner
Wer mit der Weserfähre von Bremerhaven nach Nordenham übersetzt, muss sie sehen: Rund und riesig ragen rostbraune Stahlteile am Nordenhamer Ufer in den Himmel. Die Kolosse besitzen Durchmesser bis um die zehn Meter und sind bis zu rund 80 Tonnen schwer.
Hier vor dem Werk von Steelwind Nordenham sind sie unübersehbar. Doch irgendwann werden sie großenteils unsichtbar sein. Dann stecken sie tief im Meeresboden. Ein Teil von ihnen ragt immerhin noch hinaus über den Meeresgrund ins Wasser und ihr oberster, gelb beschichteter Abschnitt sogar über die Wellen. Weithin sichtbar ist dann, was sie tragen: die Türme und ganz oben die Rotorblätter der Windräder, die sauberen Strom erzeugen.
Die Kolosse am Weserufer sind Teile von Offshore-Windkraftanlagen. Genauer gesagt Teile von Fundamenten der Anlagen. Die Fundamentteile werden Mantelschüsse genannt, sagt Andreas Liessem, als er in einem Büro im dritten Stock des Werkes einen Überblick über die Produktion gibt. Hier oben kann man sich noch ruhig unterhalten, bevor es später runter und raus geht zu den Mantelschüssen, die mit Holzkeilen vor dem Wegrollen gesichert werden. Und rein in die Werkshalle, in der Fahrzeuge herumkurven, schwere Lasten bewegt werden, meist von Maschinen, aber manchmal auch von Männern mit Muskeln, in der Geräte brummen und die Funken fliegen.
Liessem, der im Büro ein Business-Outfit trägt und später einen Arbeitskombi mit Reflektorstreifen, Helm und Schutzbrille, bildet mit Jost Backhaus die Geschäftsführung von Steelwind Nordenham.
In drei Schichten wird rund um die Uhr gearbeitet
In der Produktion werde werktags in drei Schichten rund um die Uhr gearbeitet und wenn es sein muss noch einmal samstags, so Liessem im Lauf des Werksbesuchs. Hintergrund des Hochbetriebs ist der Ausbau der Offshore-Energie in Deutschland und der Welt. Steelwind Nordenham hat schon Fundamente für Nord- und Ostsee, für Großbritannien, die USA und Taiwan gebaut, aktuell arbeiten sie unter anderem an Bauteilen, die später vor Polens Küste stehen werden.
Die Firma ist eine Tochter des Stahlkonzerns Dillinger Hütte im Saarland. Die Fundamente bestehen daher aus Dillinger Stahl. Die Kollegen an der Saar schicken ihn in Gestalt von Grobblechen per Schiff auf die Reise nach Niedersachsen. Über Binnenwasserstraßen geht es erst nach Rotterdam und nach dem Umladen auf Küstenmotorschiffe nach Nordenham.
Die Grobbleche sind Stahlplatten von einer Dicke bis 120 Millimeter, was ungefähr vier normalen Tischplatten übereinander entspricht. Die Nordenhamer verwandeln die Grobbleche in Mantelschüsse und setzen die Mantelschüsse zu Fundamenten zusammen.
Zwei oder drei Bleche werden zu einem „Mantelschuss“ verbunden
Gerafft geht das so: Je zwei oder drei Bleche verbinden die Arbeiter zu einem sogenannten Mantelschuss. Erst „heften“ sie die Bleche, das heißt schweißen sie provisorisch zusammen. Dann schweißen sie die Nähte richtig zusammen. Anschließend biegt eine Maschine mit Walzen die Bleche zu einem Zylinder. Daraufhin werden die Nähte noch von außen verschweißt. Fertig ist der Mantelschuss, genauer gesagt der zylindrische Mantelschuss, denn es gibt auch konische, deren Fertigung etwas anders abläuft. Mantelschüsse sind die runden Kolosse, die am Weserufer stehen, das als Pufferlager genutzt wird.
Aus mehreren Mantelschüssen bauen die Arbeiter eine Sektion – wieder durch Schweißen innen und außen. Aus einer Handvoll Sektionen entsteht ein Fundament. In dem stecken letzten Endes rund 30 Mantelschüsse. Diese sind inzwischen zu einer enormen Röhre gewachsen, bis zu 120 Metern lang und 2400 Tonnen schwer.
Steelwind bietet zwei Sorten Fundamente an: Sogenannte Monopiles, die quasi nur eine große Röhre darstellen, sowie die aufwendigeren und schwereren Single Piece Foundations.
Die aus nacktem Stahl bestehenden Fundamente fahren schließlich auf Schienen in eine zweite Halle zum Strahlen und Beschichten. Eine Beschichtung brauchen die oberen Abschnitte, die dem Meer und der Luft ausgesetzt sein werden. Der unterste Abschnitt braucht keine Beschichtung, erklärt man im Werk. Er werde bis zu 30 Meter in den Boden gerammt – dort komme kein Sauerstoff mehr hin, der ihn rosten lassen könnte.
Die Fertigung ist aufwendig
So sieht die Fertigung des Fundaments made in Germany in Kurzform aus. In Wirklichkeit ist sie um einiges aufwendiger.
Viele Schritte und großes und kleines Gerät stecken dahinter. Außerdem Kräne mit Haken und Elektromagneten sowie kuriose Fahrzeuge wie die Selbstfahrer-Modultransporter (SPMT), an Tausendfüßler erinnernde lang gestreckte Auflieger mit zig Achsen, oder ein Portalhubwagen, der die Mantelschüsse ans Weserufer und zurück transportiert. Aber vor allem stecken hinter der Fertigung die Schweißer, Stahlbauer, Schlosser und anderen Facharbeiter mit ihrer Erfahrung und Expertise.
Einen Eindruck davon bekommt man, wenn man dem stellvertretenden Schichtleiter Andre Heidemann und seinem Kollegen vor die Füße guckt. Dort bewegt sich eine komplizierte Apparatur etwas schneller als eine Schnecke mit knisterndem Geräusch über die Verbindung zwischen zwei Grobblechen. Vorne weist ein roter Laserstrahl die Richtung, dahinter stoßen Düsenköpfe den Schweißdraht aus. In der Fuge hinterlässt die Apparatur eine glühende Naht.
Das Blech wird angebogen und zu einem Zylinder gewalzt
Es handelt sich um eine Unter-Pulver-Schweißanlage, erklärt Heidemann, der fast den gleichen Arbeitskombi wie sein Chef Andreas Liessem trägt, nur dass der von Heidemann nicht so neu und sauber strahlt. Die Anlage füge die ersten Bleche zusammen, die später einen Mantelschuss ergeben. „Das macht der Kollege jetzt gerade halt fertig, der schweißt die Naht.“ Dann werde das Blech zur Biegepresse geschickt, angebogen und später zu einem Zylinder gewalzt, so Heidemann.
Der Arbeitsort vieler Männer richtet sich an den riesigen Teilen aus. Sie steigen zum Beispiel mit Schweißmaschinen in die halb fertigen Röhren, um von innen zu schweißen. Oder sie fahren mit dem Fahrstuhl auf eine Arbeitsbühne, um von außen zu schweißen. Die Mantelschüsse drehen sich dabei langsam um die eigene Achse. Die Schweißnaht wächst so den Männern gleichsam unter den Händen hervor.
Das Fundament bekommt im Werk auch Löcher – absichtlich. Manche seien Wasserausgleichslöcher, erklärt die Geschäftsführung, denn der Abschnitt, der im Meer stehen wird, füllt sich auch mit Meerwasser.
Eine besondere, bisher nur als Kontur sichtbare Öffnung zeigt Schlosser Alexandru Mitran. Er arbeite seit sieben Jahren im Werk, erzählt der Mann mit dem rötlichen Vollbart freundlich. Dem Akzent nach gehört Mitran zu den aus dem Ausland stammenden Mitarbeitern, es seien zum Beispiel viele Polen bei Steelwind, sagt Geschäftsführer Liessem. Der Schlosser weist auf die künftige ovale Öffnung im Fundament. Dort kommt mal eine Tür rein. Durch sie werden später die Techniker die Windkraftanlage betreten und verlassen. Dann, wenn die Stahlriesen vom Weserufer weit draußen im Meer stehen.
Die Offshore-Windparks vor der deutschen Küste
Windräder Vor Deutschlands Küste waren zum Jahresende 2024 nach Branchenangaben 1639 Windräder in Betrieb. Ihre Leistung betrug zusammen rund 9,2 Gigawatt, wie das Branchenunternehmens Deutsche WindGuard Anfang Februar 2025 mitteilte. Etwa 7,4 Gigawatt entfielen auf die Nordsee und 1,8 Gigawatt auf die Ostsee. Über die Netzanschlüsse ließen sich die Anteile auch den Bundesländern zuordnen, nämlich Niedersachsen 5,3 Gigawatt, Schleswig-Holstein 2,1 Gigawatt und Mecklenburg-Vorpommern, wo die gesamten Ostsee-Windräder angebunden seien, 1,8 Gigawatt.
Rotordurchmesser In den vergangenen Jahren haben Größe und Leistung der Windräder zugenommen. So besitzen die bisherigen Offshore-Anlagen samt den 2024 neu zugebauten im Schnitt einen Rotordurchmesser von 136 Metern, hat die Deutsche WindGuard errechnet. Bei den 2024 zugebauten Anlagen allein liege der Durchschnitt schon bei 182 Metern Rotordurchmesser. Die durchschnittliche Leistung stieg demnach von 5,6 Megawatt auf 10,2 Megawatt pro Anlage.